Traditional Sardinian handwoven textiles are uniquely beautiful in their design and creation. The artistry and the intrinsic quality of the handmade are apparent. The textiles carry the anima, or spirt, of the weaver and the island.
Your appreciation of this grows when you understand how the weavings are created.
Whether it’s done in the home or studio, handweaving is demanding and time-intensive. It requires patience, engineering skill, and physical strength. Weaving involves many steps, and progress is slow. The weavings are made with care, attention, and respect for the old ways. The results — rugs, wall hangings, tablecloths, bedspreads, pillow shams, bags, and more — are unparalleled.
The most unique and famous Sardinian handwoven textiles are found in Samugheo, in the center of the island. Other areas of Sardinia have distinct styles of weaving, stemming from the different land, climate, and types of looms available.
No matter the area or century, the handweavers and carriers of the tradition have been, and are, women, tessitrici artigianali: Strong, independent, caring, hard-working, dedicated masters of their art.
This page presents the traditions of the three towns best known for their weaving. A map is at the bottom of the page. Scroll down to read all, or click a link to jump to a specific section.
- Samugheo is in the center of the island, and handweavers here use horizontal hand looms to fashion pibiones and intricate patterns in various natural fibers.
- Nule is high in the mountains and handweavers here use vertical hand looms to weave complex patterns, stripes, and geometrical designs in wool.
- Aggius is inland in rocky Gallura, and weavers use horizontal hand looms to weave diverse patterns and stripes in wool and cotton.
Samugheo
The best known of the traditional Sardinian weavings are those from Samugheo. These distinctive textiles are often patterned with small raised bumps of thread called pibiones. Each pibione must be counted and wound by hand, one pibione at a time, one row at a time, matched against patterns marked by hand on graph paper. In addition to the raised pattern of the pibiones, the base fibers (warp) of the textile create a second and complementary pattern.
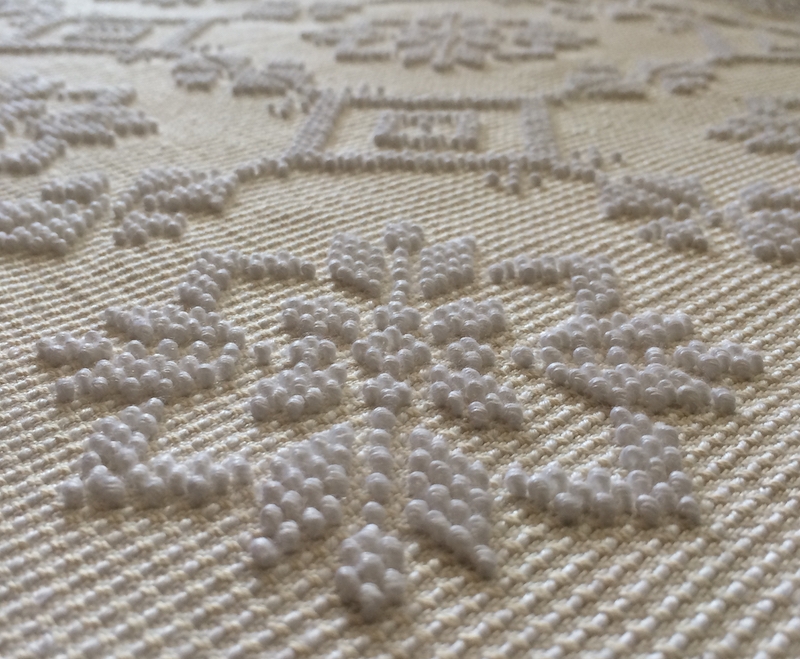
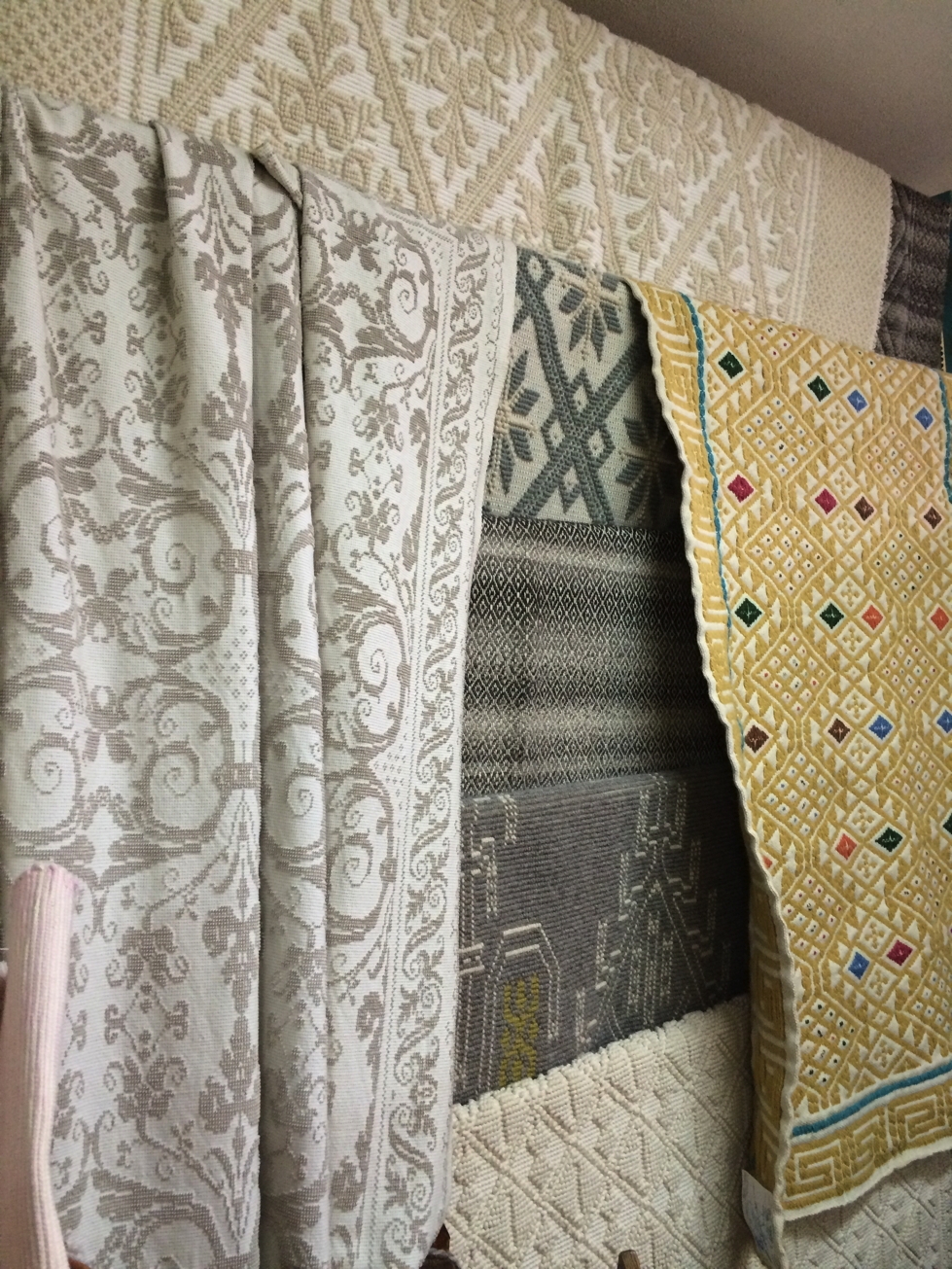
Handweavers in Samugheo — historically and always women, tessitrici artigianali — use horizontal looms, weaving with a variety of fibers. Cotton is now generally used for warps. Linen is now less used as a warp, and more often for pibiones. The weft is generally of wool and cotton.
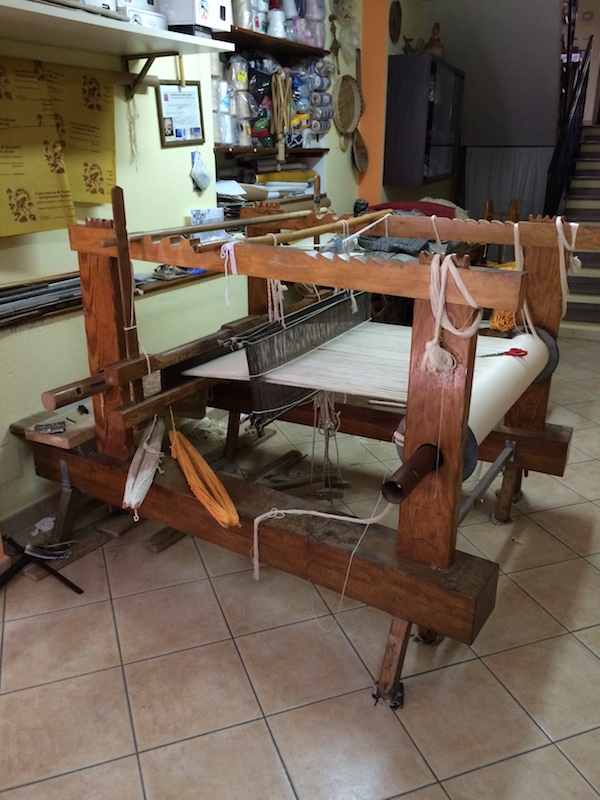
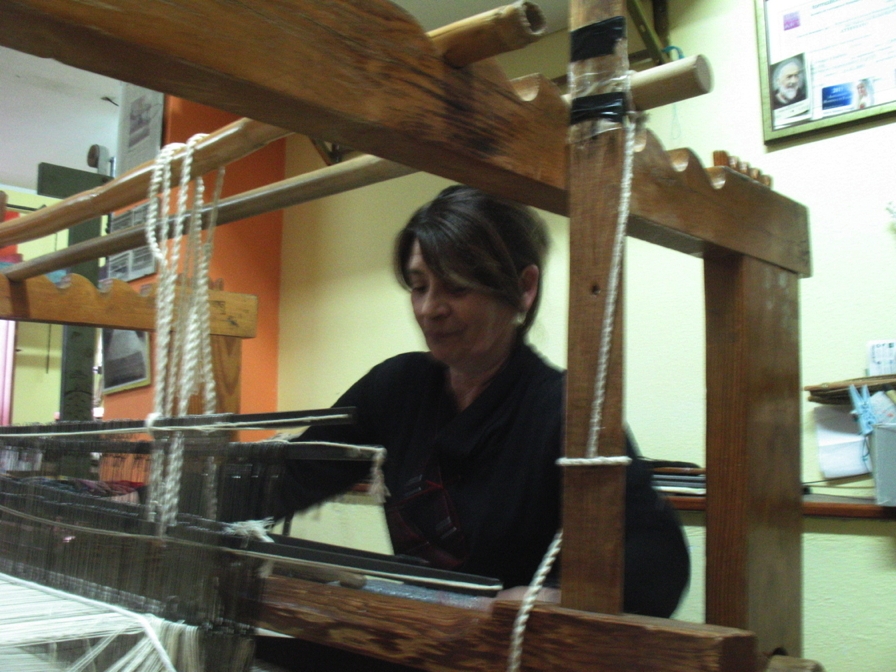
A weaver making a bedspread on a medium-sized loom counts and hand-threads 4800 warp threads, tens of thousands of pibiones, and hundreds of thousands of warp and weft fiber passages — all counted and tracked by hand, eye, and graph paper.
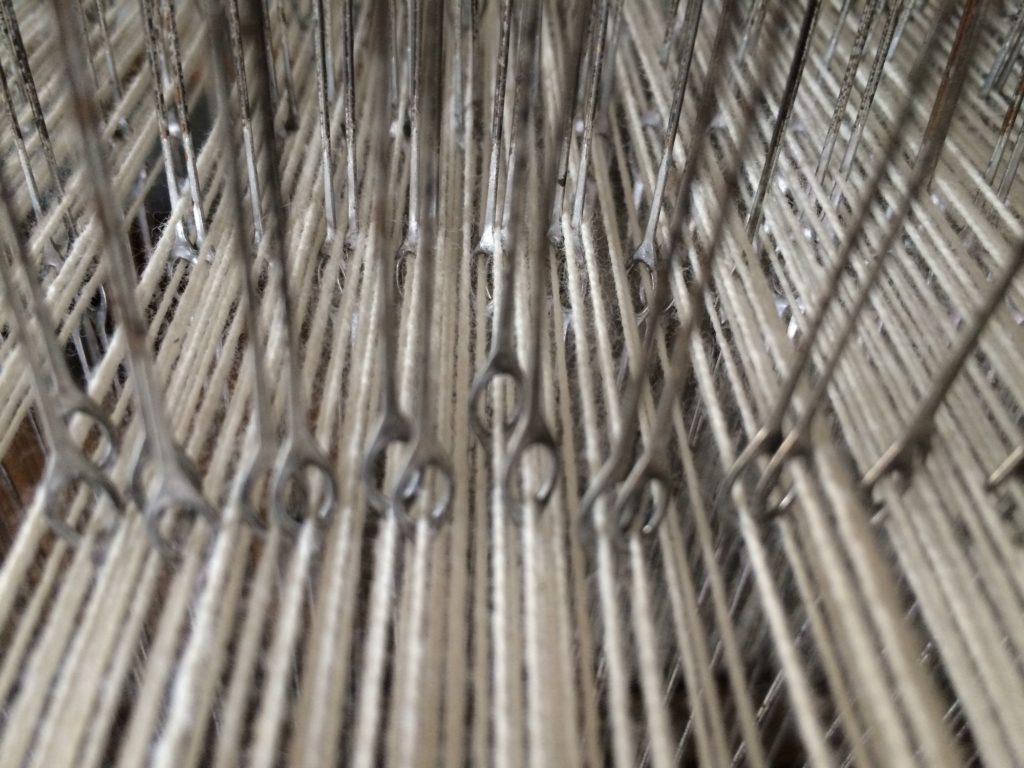
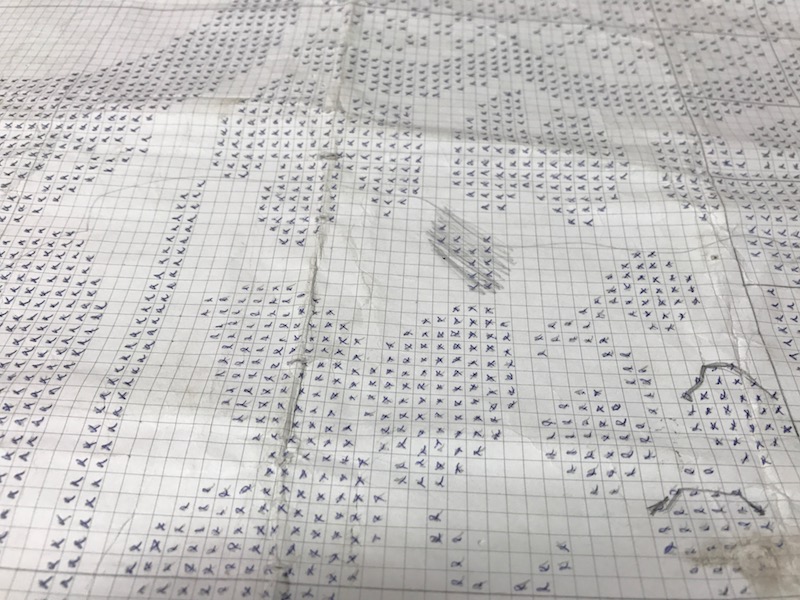
If a weaver looses count of the pibiones or the warp fibers, she must recount from the last known position. And before even starting the actual weaving process, the weaver must set up (warp) the loom, a delicate and precise but demanding process.
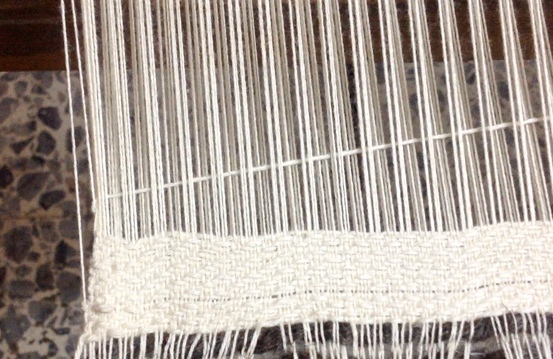
Looms operate on a system of levers and pulleys which must be perfectly assembled, balanced, and aligned. A weaving can be wrecked by one thread out of sequence, a warp that is a sixteenth of an inch off level, or pulleys that are a tad too tight or too loose.
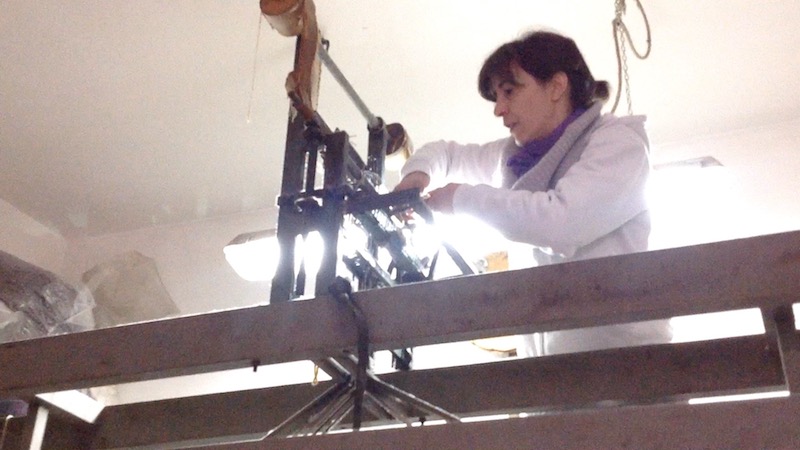
It’s not uncommon for the women to climb on or crouch under looms to tighten, loosen, balance, and align pulleys, levers, and other pieces of the loom. Weavers don’t always sit when doing the actual weaving, and even when they do, moving the beater bar to finish each row of the weaving takes a good bit of strength. Larger looms require two, three, or four standing women to pull the beater bar after each row of weaving is completed.
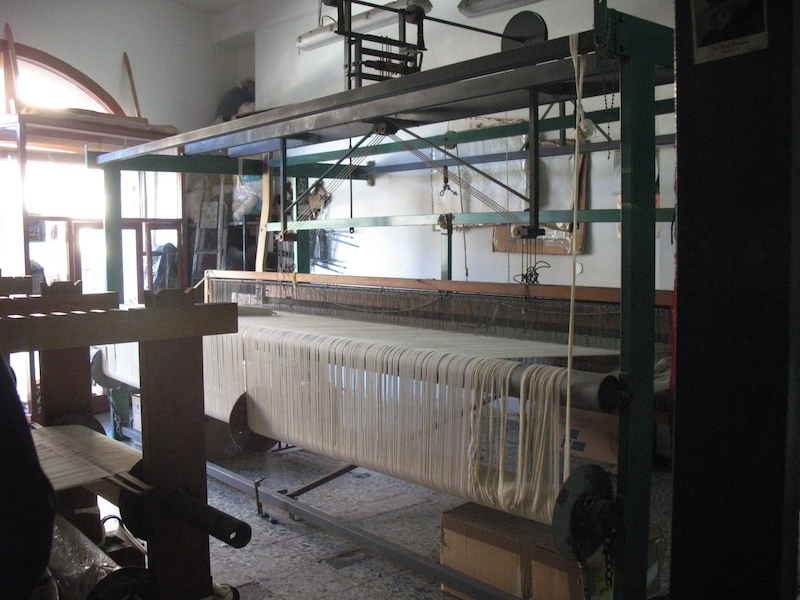
In Samugheo, only one studio, that of Isabella Frongia, still uses only hand-powered looms — even the large loom, about three meters long, used for making large room-sized rugs — is entirely hand-powered and hand-operated. (The other studios in Samugheo converted to hydraulic power looms about 50 years ago, and there are even several automated factories).
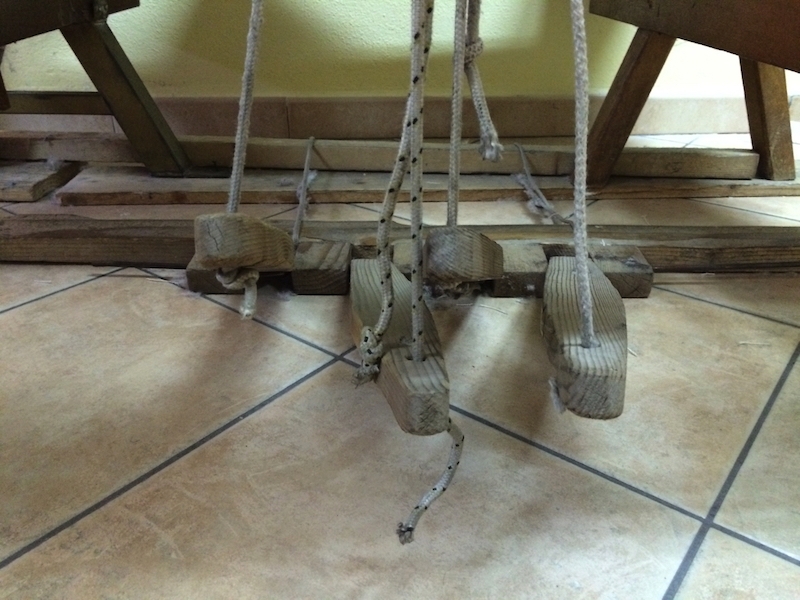
When you experience the process, grasp the time it takes to weave something by hand, and understand the mental skill and the physical work involved, you appreciate more fully the beauty and detail in each row of an expertly handcrafted textile. The artistry becomes more perceptible, more personal. You realize the finished textile you have in your hands is not just an object, but a creation born of the skill, concentration, and love of the weaver.
Learn more about the weavers on the page Isa Frongia Studio: Isa, Susanna, and Anna Maria.
Watch the short documentary I Want to Weave the Weft of Time to see these women in action!
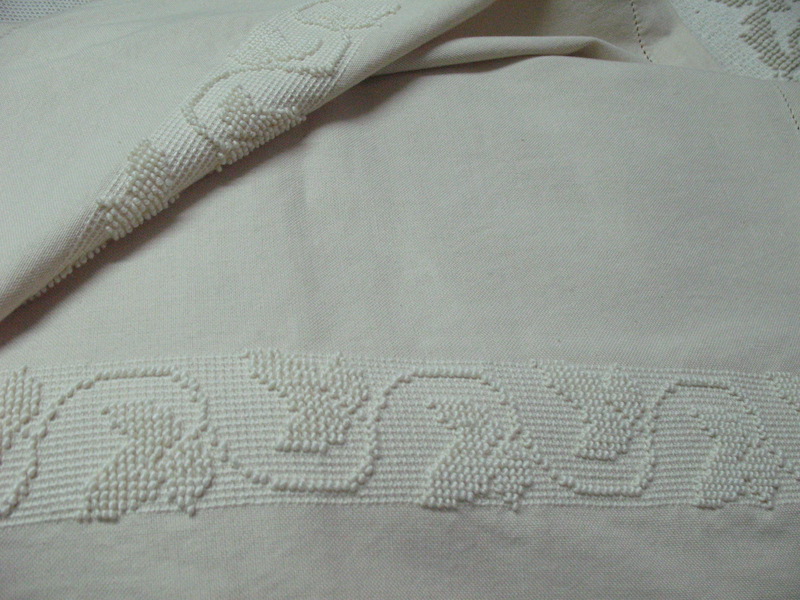
Nule
Nested between mountains and hot springs in north central Sardinia, the town of Nule lies on a high plain more than 2000 feet above sea level. The cool, steep atmosphere lends itself to sheep and, of course, their wool, prized by weavers within and beyond Sardinia.

This wool, spun and dyed into a distinctive color pallet and woven into designs typical of the town are the characteristic features of Nule’s traditional textiles.
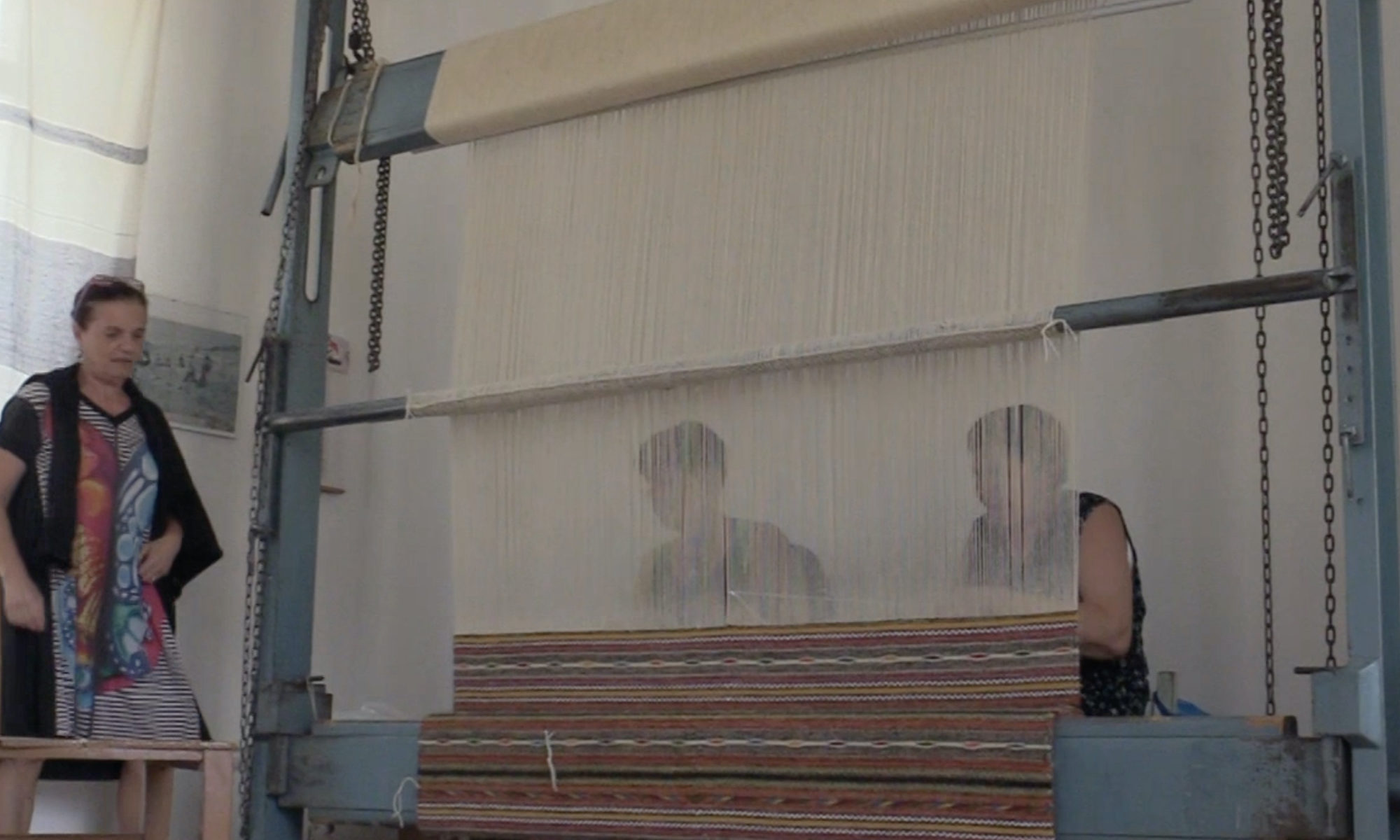
Weavers in Nule — always women, tessitrici artigianali, as across Sardinia—use vertical looms rather than the horizontal looms found in other areas of Sardinia. This is significant because the type of loom dictates the techniques a handweaver uses, the types of designs she makes, the weaves she employs, and more. (In fact, each type of loom produces a characteristic sound as the weaver works, and a knowing listener can discern merely by sound whether a weaver’s using a vertical loom or horizontal loom (hand-powered or hydraulic), and sometimes even the particular pattern being woven!)
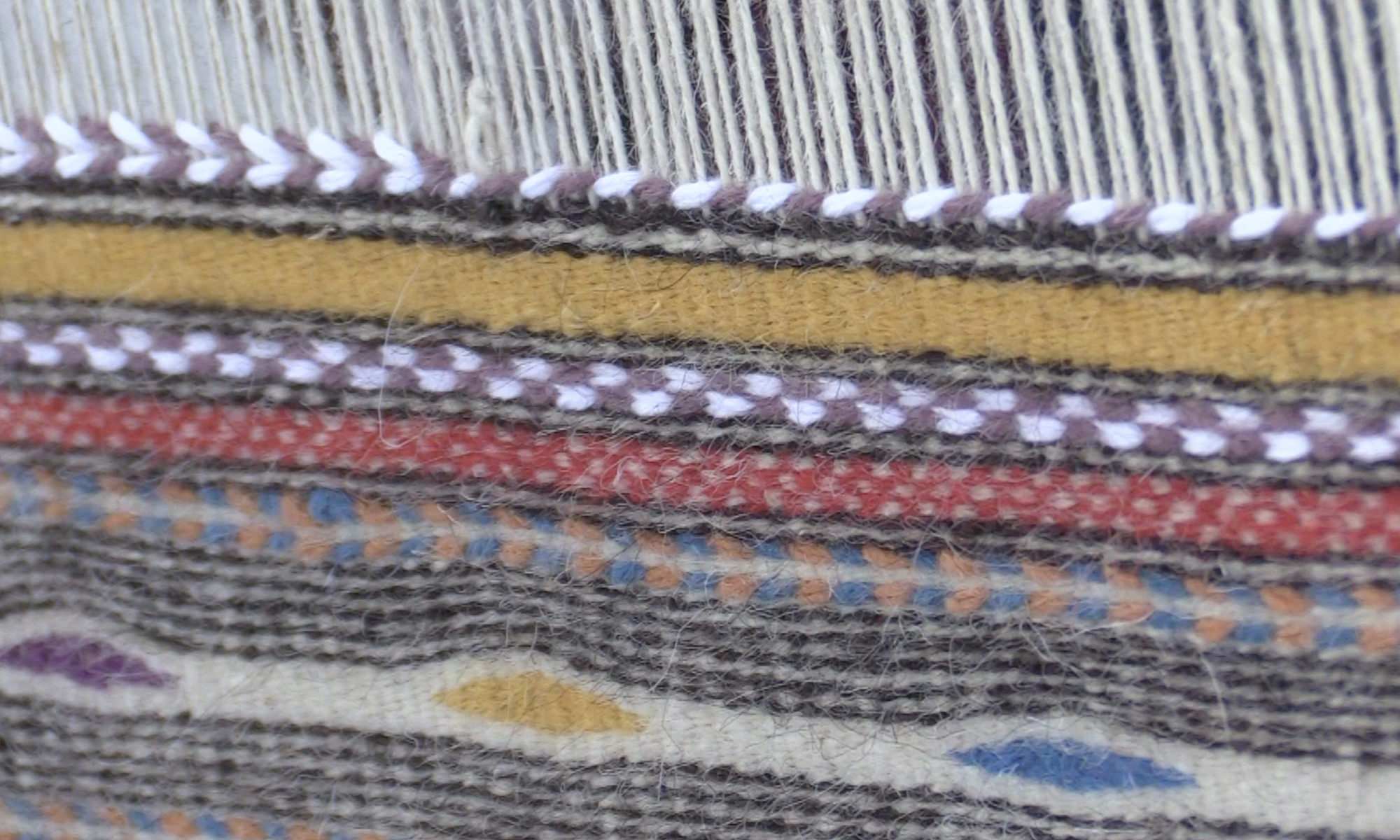
Vertical looms are so named because warp fibers (the structural foundation of the textile) are run up and down, like strings of a harp. The women move their fingers through the warp fibers in a plucking motion to pass the weft fibers (the threads woven into the warp) back and forth, building the weaving from the floor upwards.
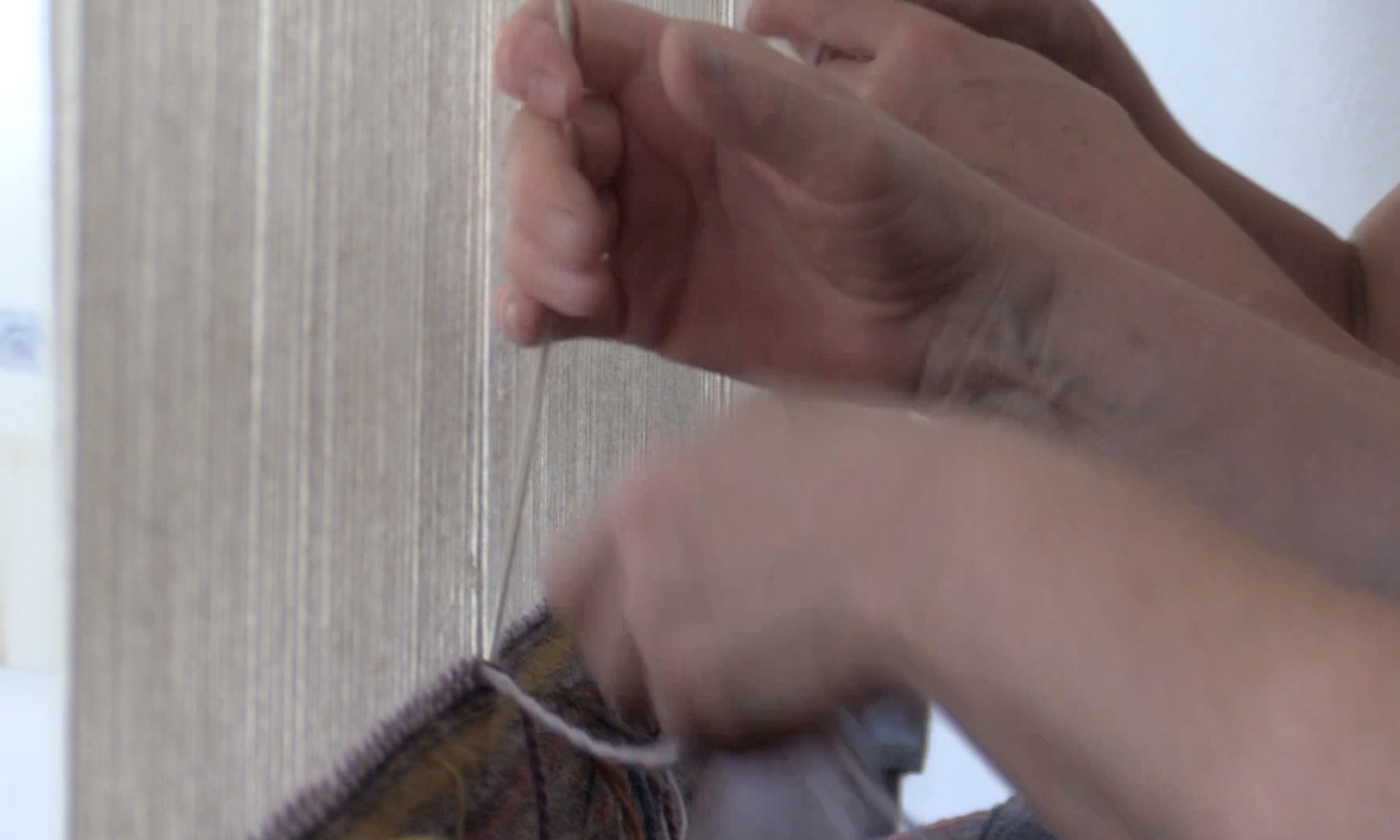
A wool warp is also characteristic of Nule, as weavers in other areas tend to use cotton or sometimes linen warp fibers. The combination of wool warp and weft, tightly beaten, makes Nule textiles extremely dense.
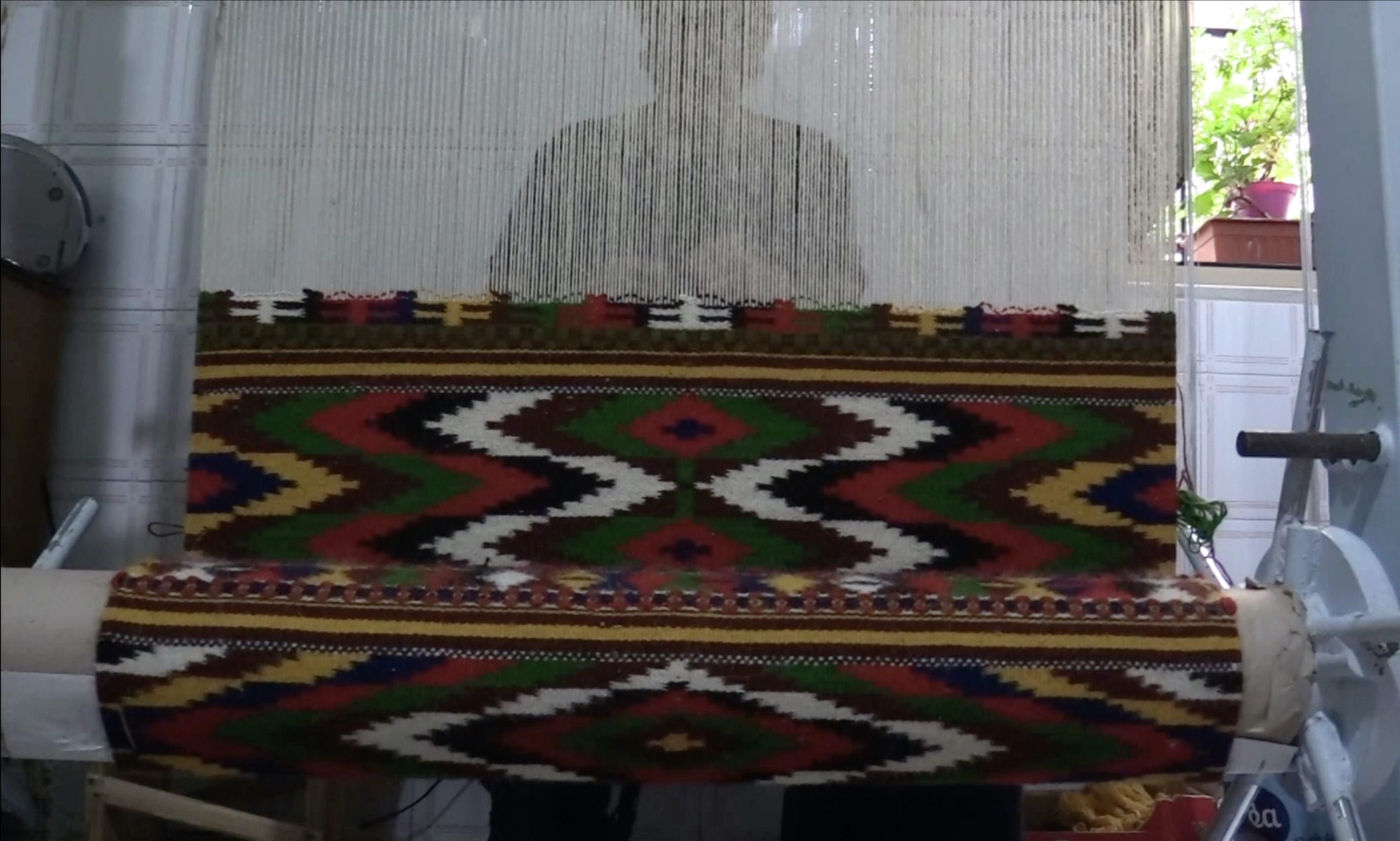
The colors used in the textiles are often arranged in traditional named sequences. Designs are usually geometrical, and sometimes placed in stripes. Some say the color sequences and designs have nearly-forgotten and perhaps esoteric meanings.
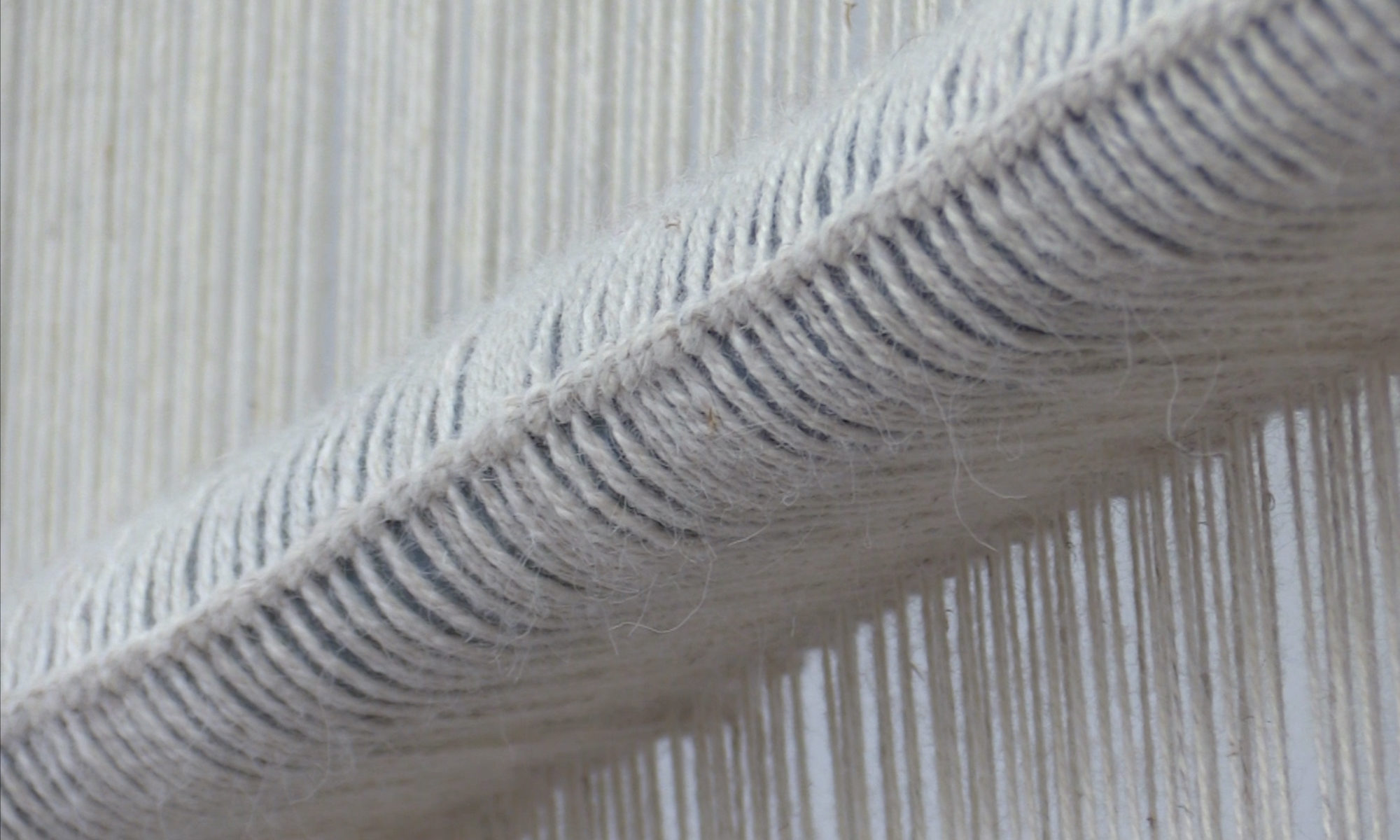
Before weaving the weft, the weavers must warp the loom: They wind woolen fibers around an adjustable bar in the middle of the loom, using measured wrapping and a loose knot-like structure to create even spaces between each warp fiber. After this structure is created on the middle bar, the ends of the warp are wound around rolls at the top and bottom of the loom. Warp tension is regulated by adjusting levers on the top or bottom crossbars, or by inserting and moving smaller bars through the warp.
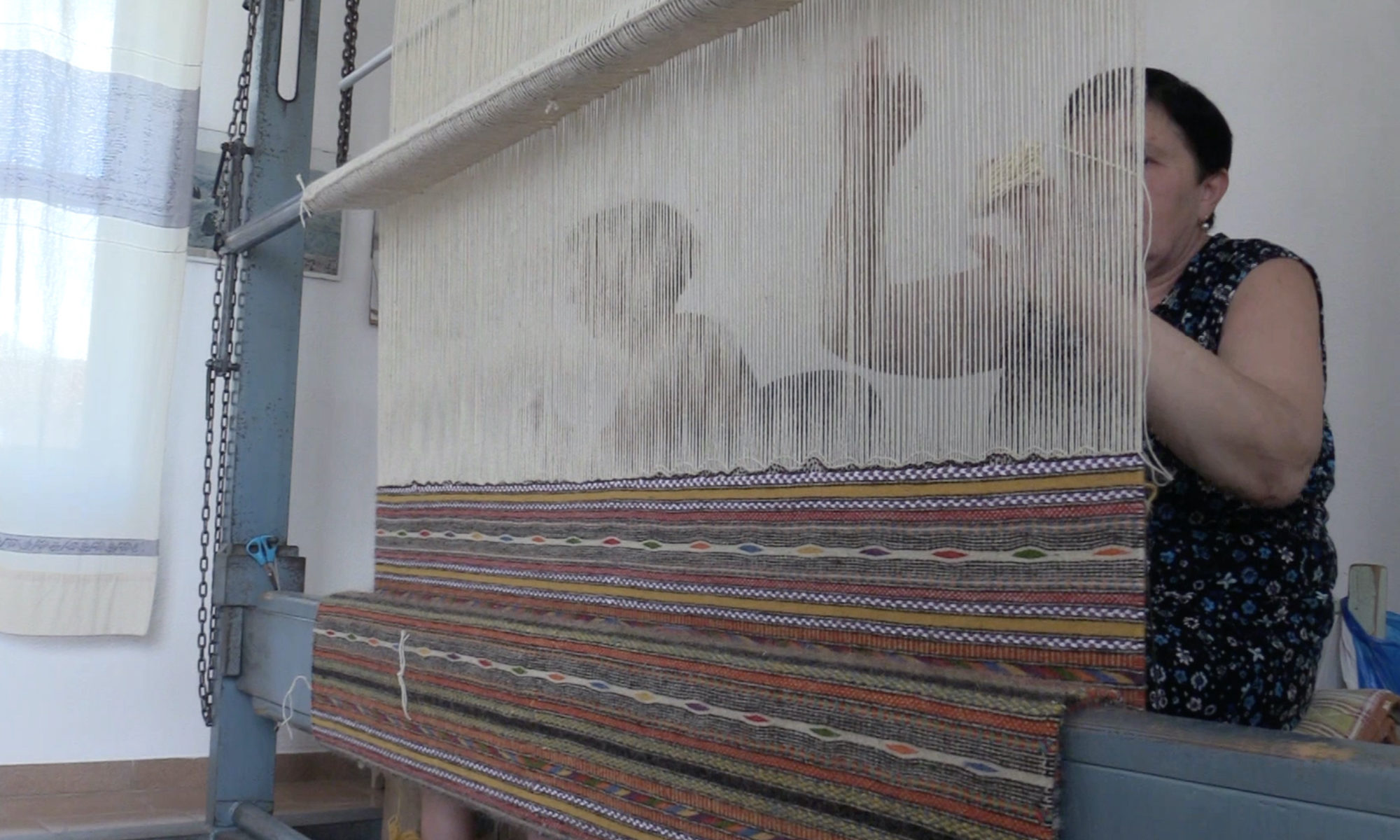
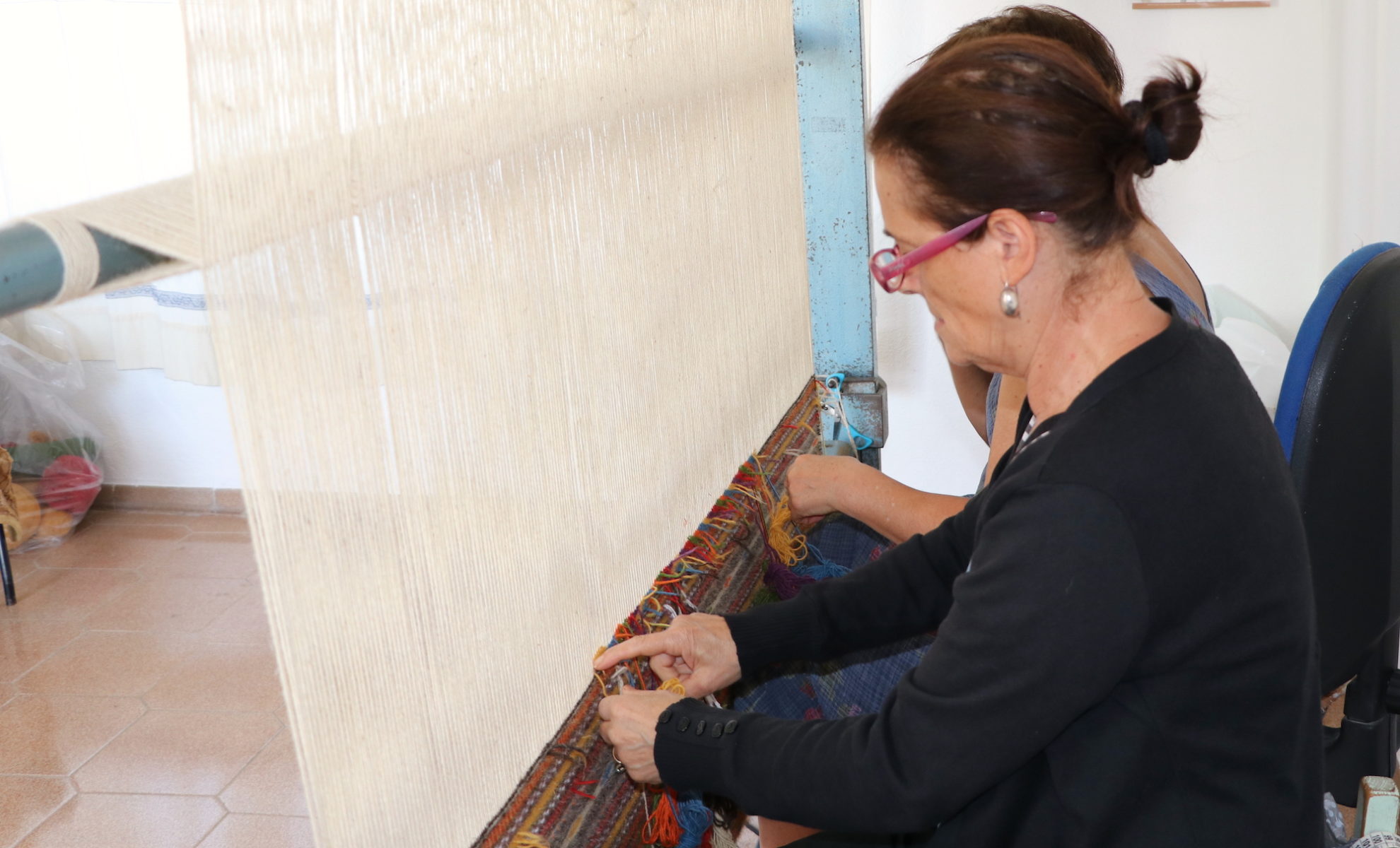
When weaving, the women generally hold the weft fibers directly in their fingers; this enables rapid movement between warp threads and facilitates changes of thread color and design that would be difficult if the women used a shuttle. After weft threads are passed through the warp, the weaver may adjust them with a finger or a small stick; she then compresses them by inserting a small wooden toothed tool between the warp threads and beating the weft threads down by hand.
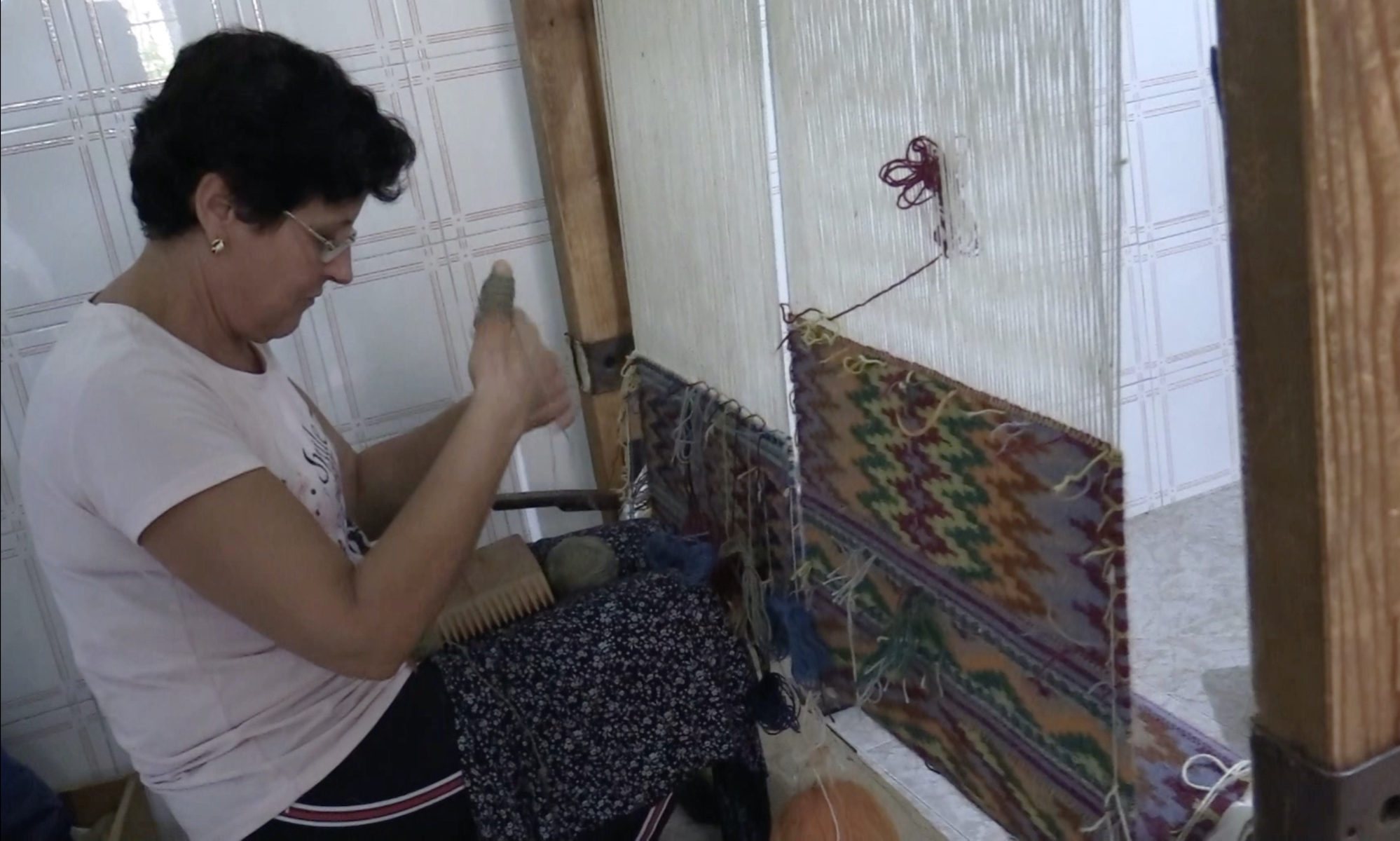
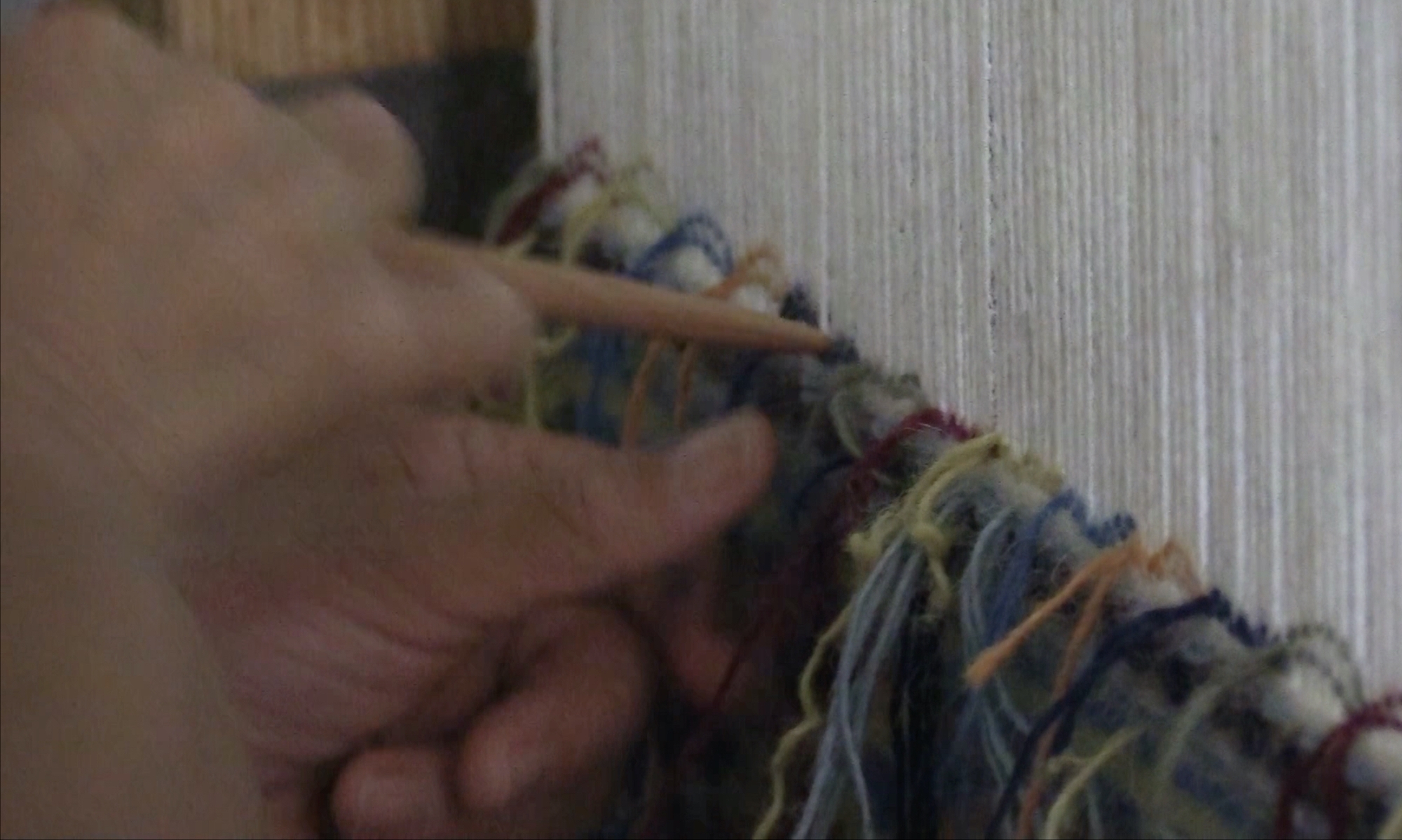
Experienced weavers move their hands so quickly that it’s nearly impossible to see their hands in motion when they weave or when they beat the textile!
While weavers generally work one row at a time to create a textile, vertical looms and the small beaters enable the women to add a small area of color or design before beating and leveling the rows of the weaving. After many rows are beaten and compressed, any dangling threads indicative of a color change are trimmed and absorbed into the density of the textile.
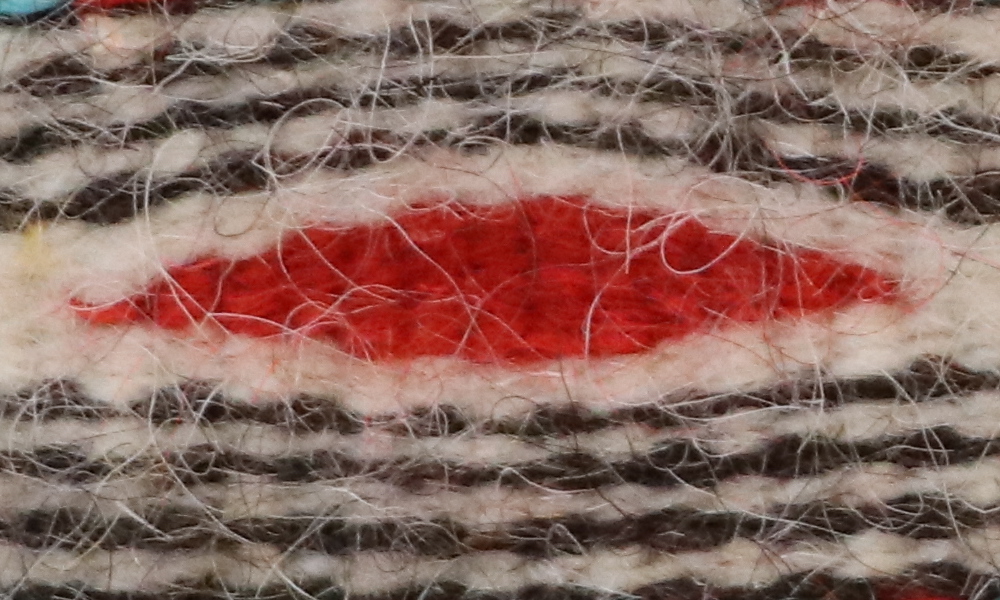
While Nule’s vertical looms are now often made of metal rather than wood, the town’s handweavers maintain the traditions, designs, and movements of their mothers and grandmothers, weaving, beating, and trimming rugs and wall hangings by hand, some even expanding on tradition to inject modern colors, designs, and items.
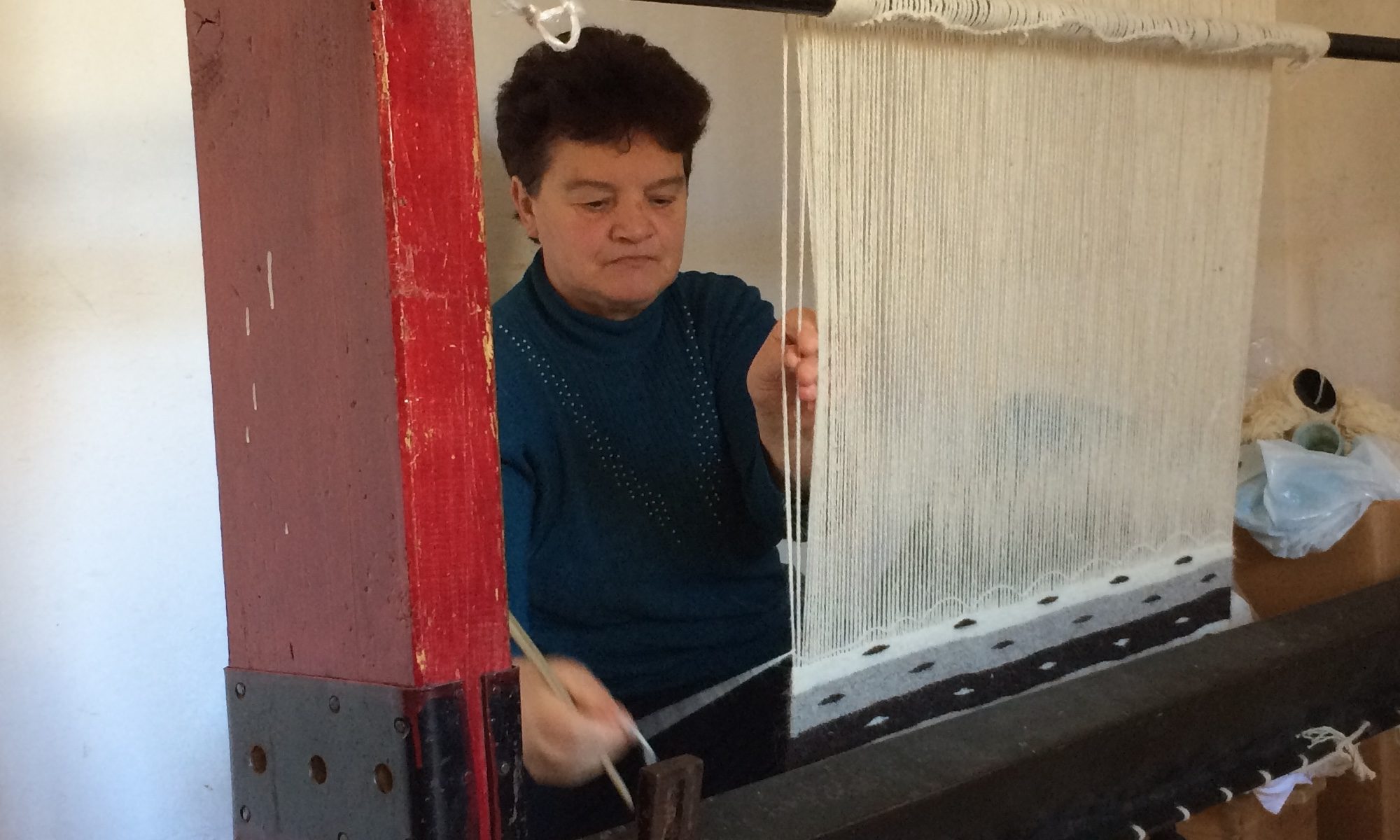
Textile designer Eugenia Pinna, the best-known of Nule’s contemporary daughters, creates timeless modern designs rooted in tradition, exhibits across Sardinia and elsewhere, and offers her textiles and other art on her website. A more traditional weaver, Giovanna Maria Campus, is known for her rugs, wall hangings, and demonstrations at local events.
Learn more about the weavers on the pages Eugenia Pinna and Giovanna Maria Campus.
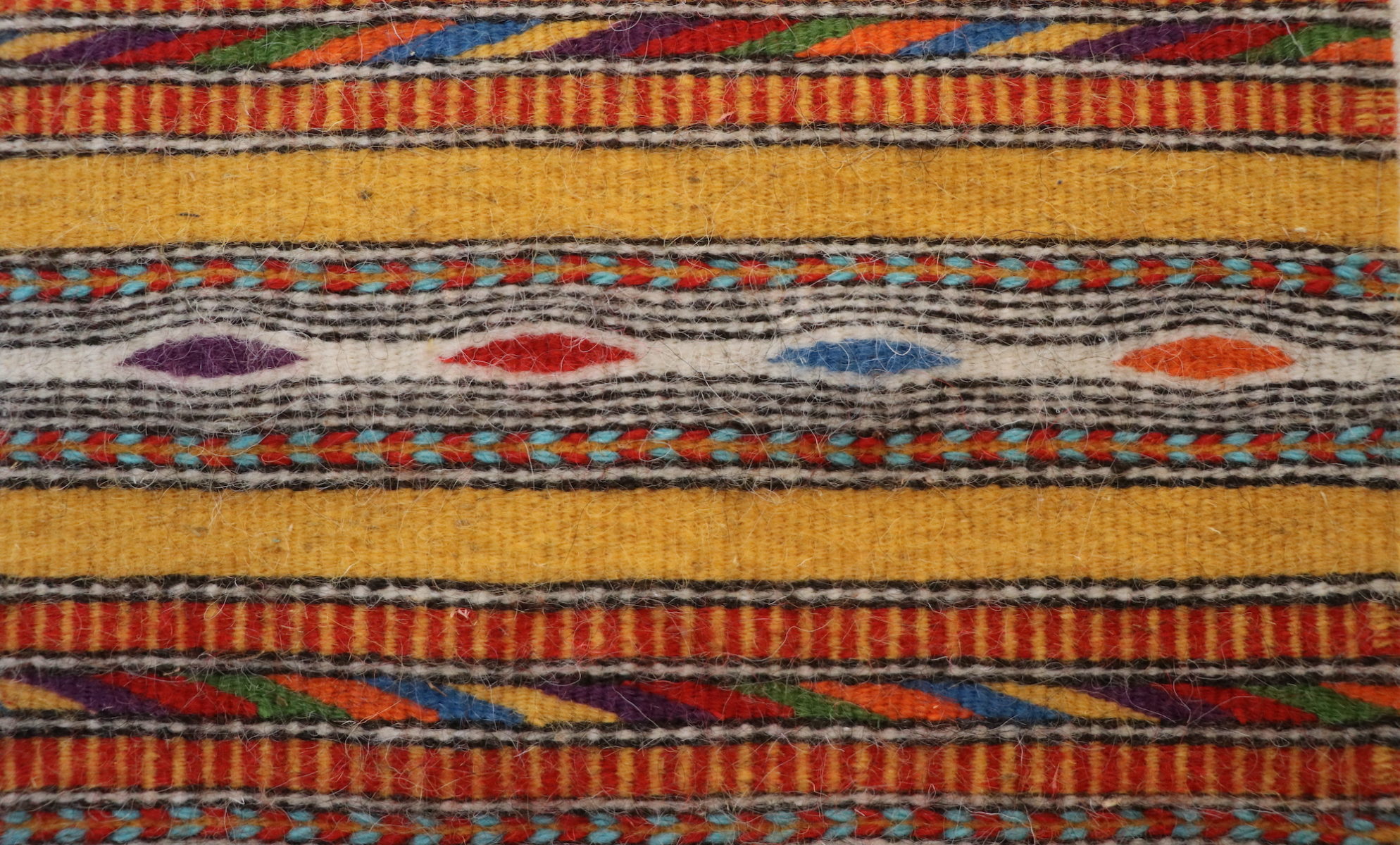
Aggius
Granite surrounds Aggius, shelters her people in cut-block buildings, and paves her streets and walkways. Ancient, tranquil, and beautiful, this small town is a hidden gem in the hills of Gallura, in Sardinia’s north. Respected for her stone and her museums, Aggius is also known for her strong textile traditions.
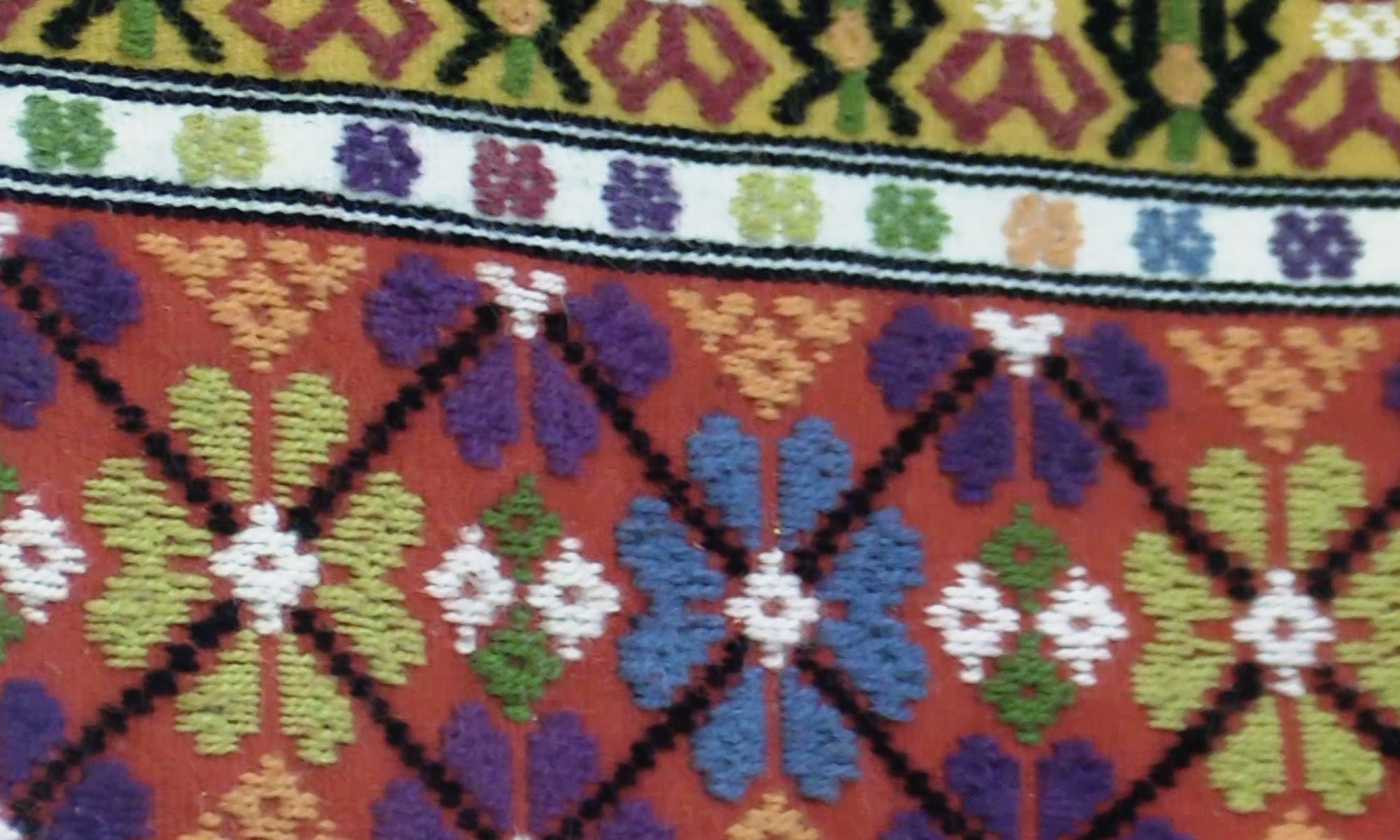
The parallels and contrasts of the land, history, culture, and art of the different regions of Sardinia are visible within Aggius and her weaving tradition. As across Sardinia, for centuries Aggius women were expected to weave their home’s textiles, even as young girls, when prepared their dowry linens. Every well-equipped house had a loom, and women from the town worked together at key times throughout the seasons to collect and prepare wool and other fibers — tedious, difficult work necessary before actually weaving.
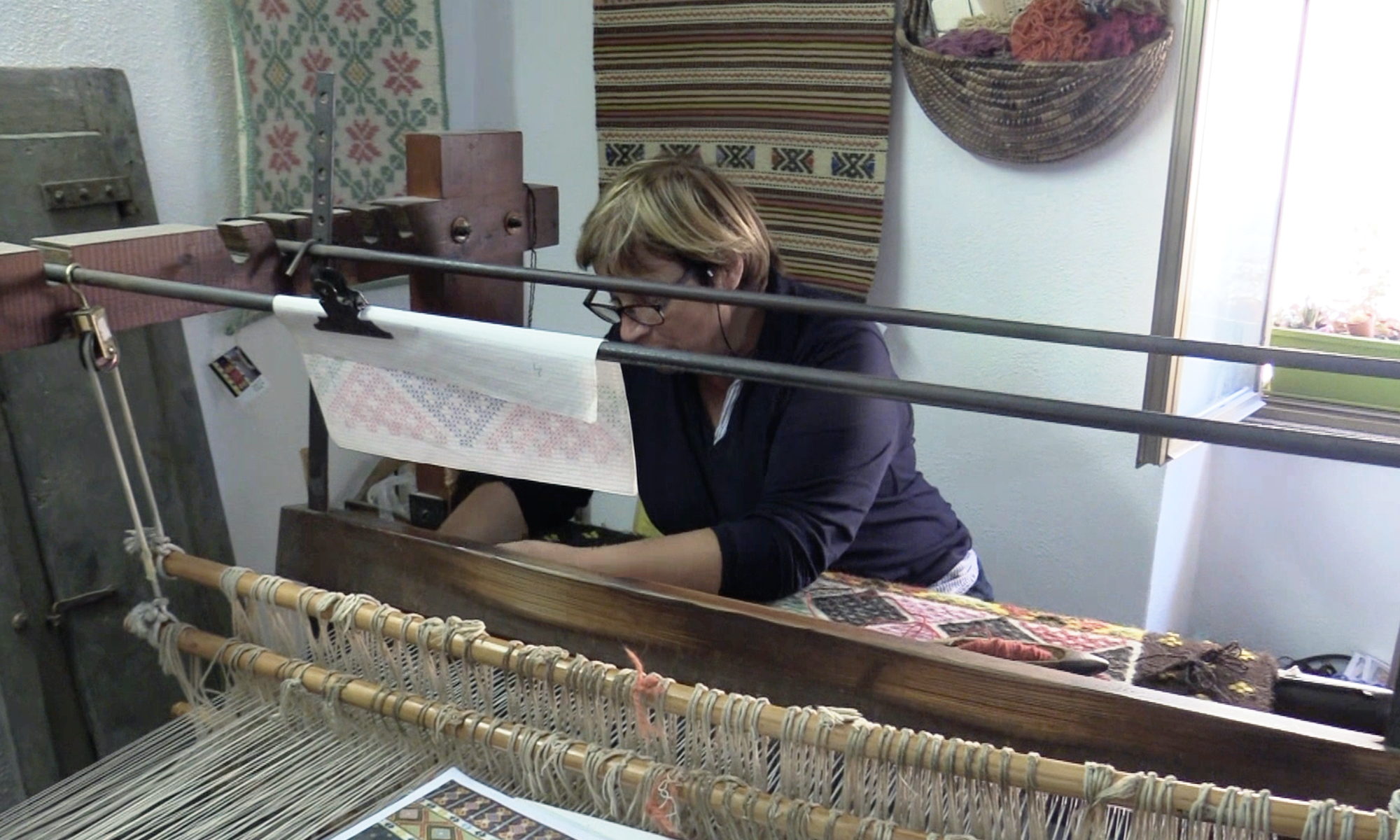
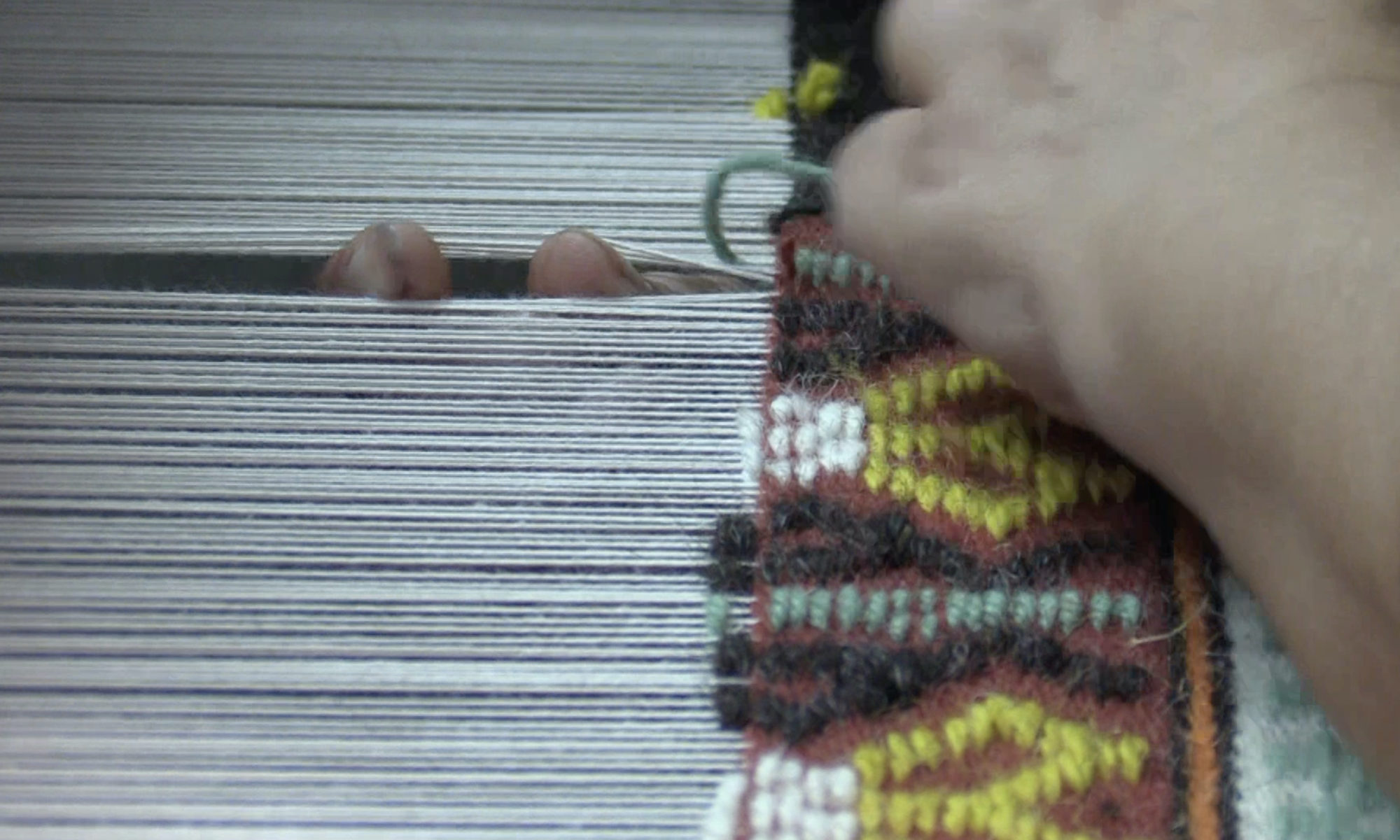
The tradition of the dowry has faded, home-handweaving is rare, and only a handful of professional handweavers remain across the island. The tessitrici artigianali in Aggius all work as their forebears did, using hand-powered horizontal looms. These looms, and their warping and setup, are similar to those found in Samugheo. The hydraulic looms that came to dominate Samugheo never arrived in Gallura, and all the weavers in Aggius work entirely by hand.
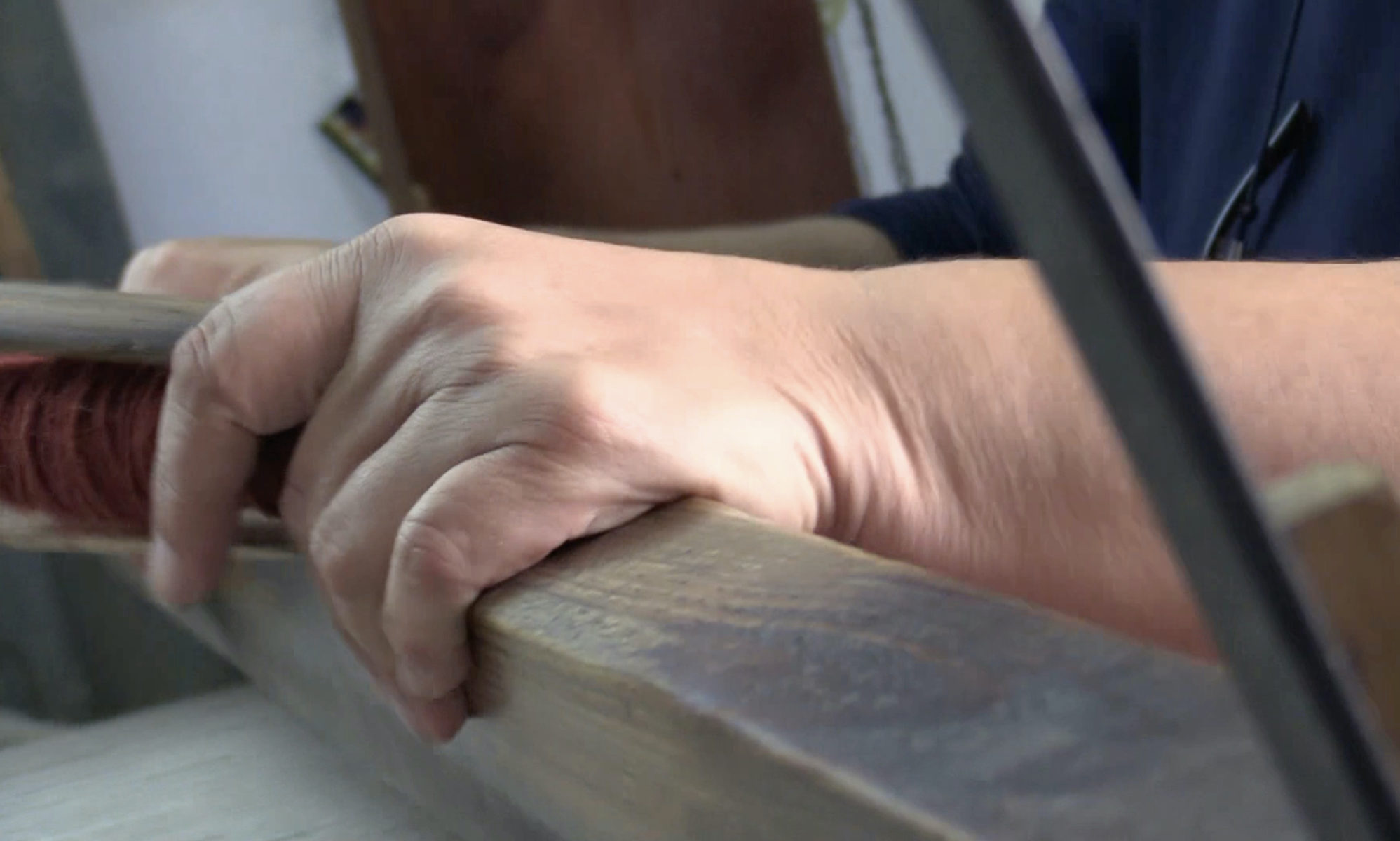
Textiles in Aggius are generally woven on a cotton warp with a wool or mixed fiber weft. Wall hangings, chest-covers, and saddle bags are common; rugs are as well, a later addition, as many houses across the island were not paved until the mid-twentieth century.
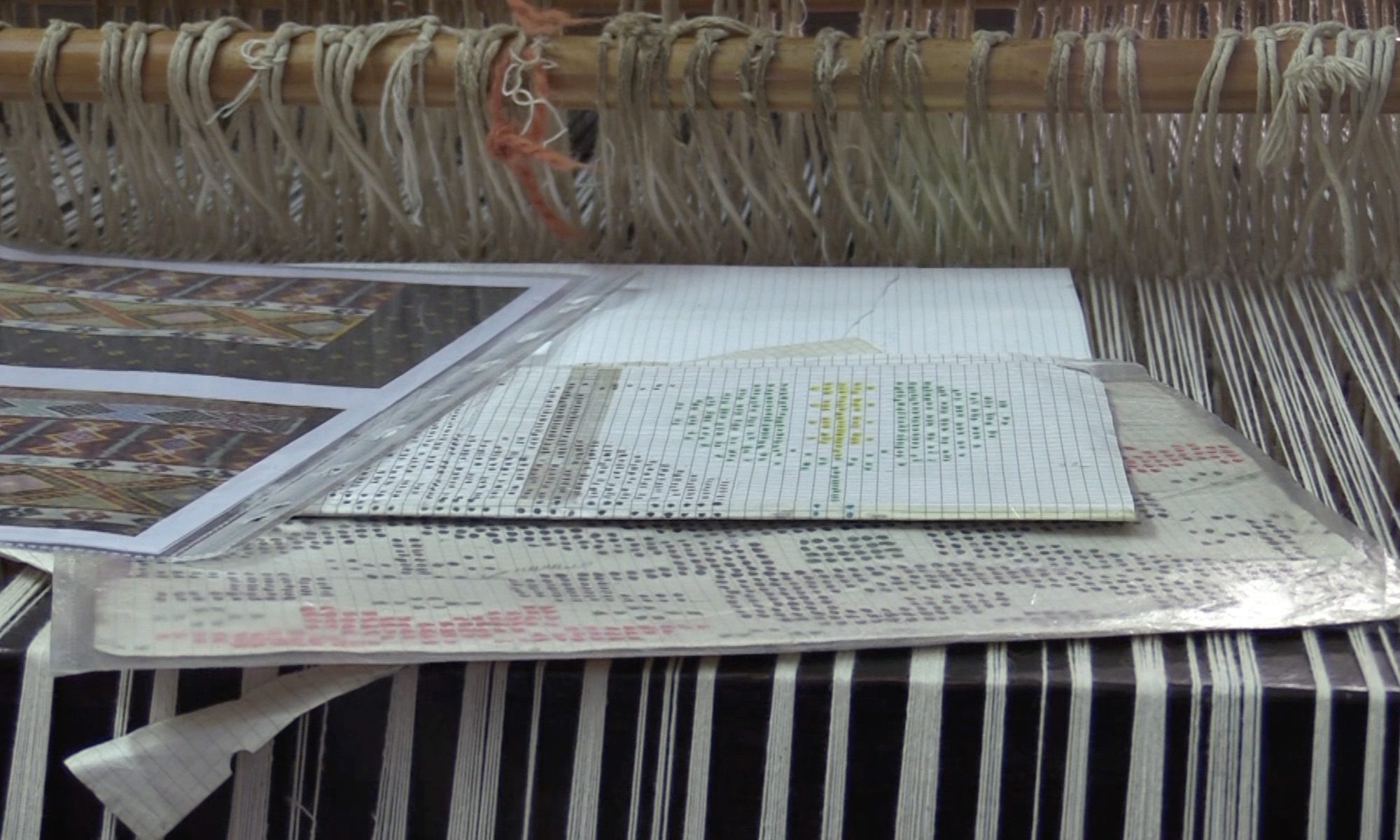
The weavings characteristic of this small town generally use flat weaves accented with a typical Sardinian wrapped weave. Pibiones are not traditionally found in weavings of Aggius.
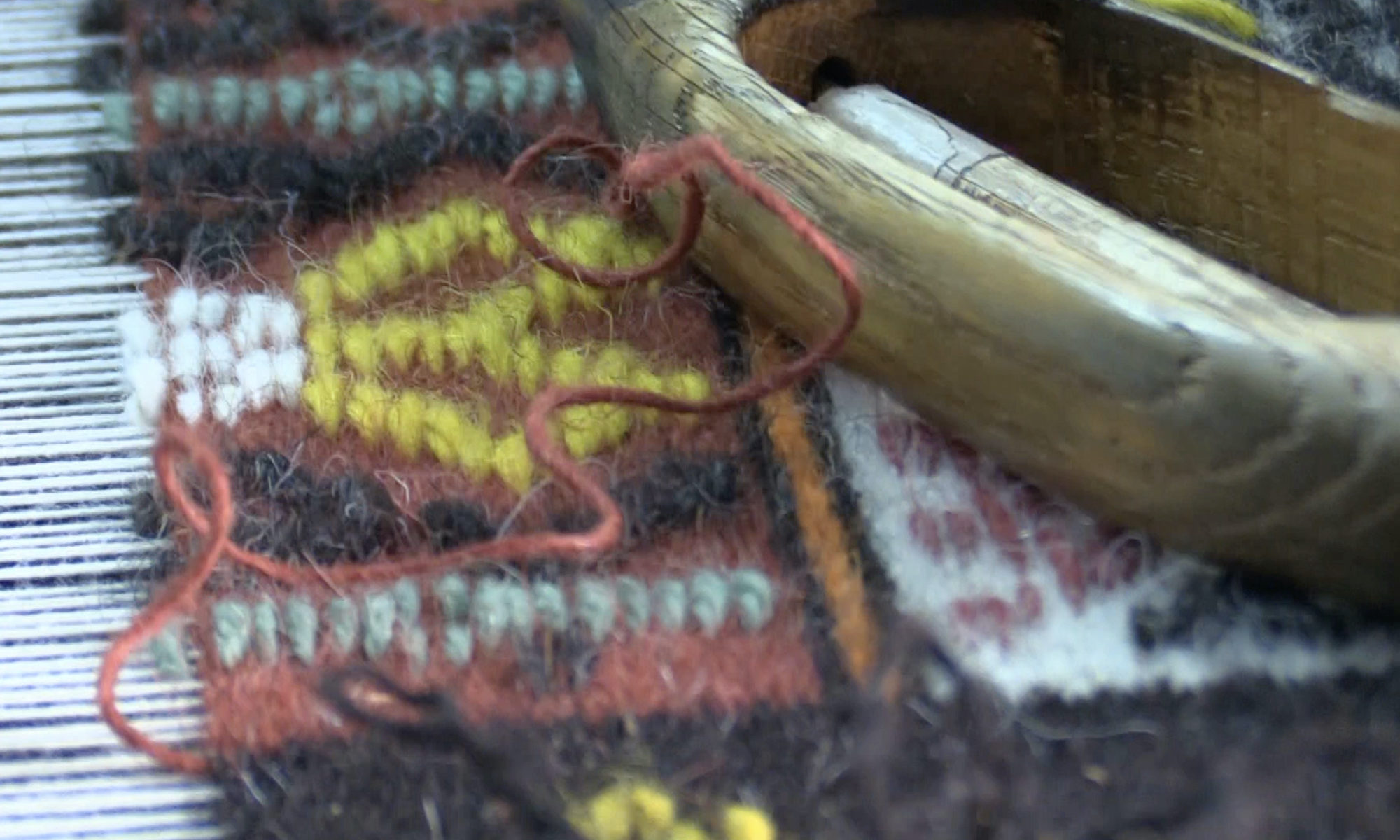
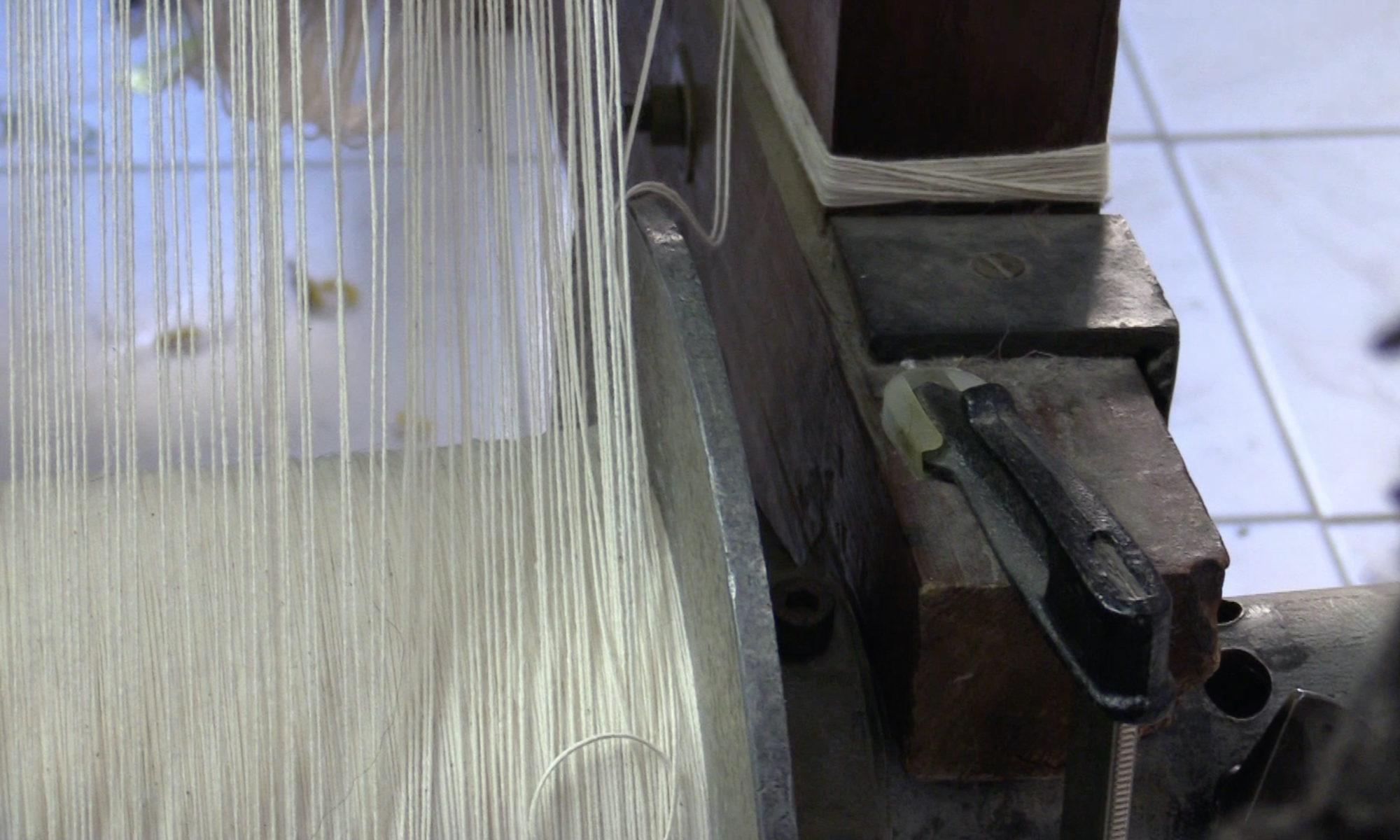
Designs are historically geometrical or based in nature; birds and flowers are common, often as a border and sometimes within an entire textile. Striped patterns and colors typical of the region distinguish the textiles. A beautiful lavender dye created from local lichen is beloved by locals and visitors, as are bright colors complemented by a refined pallet of natural Sardinian sheep wool, blended into beautiful shades of grey, black, and white.
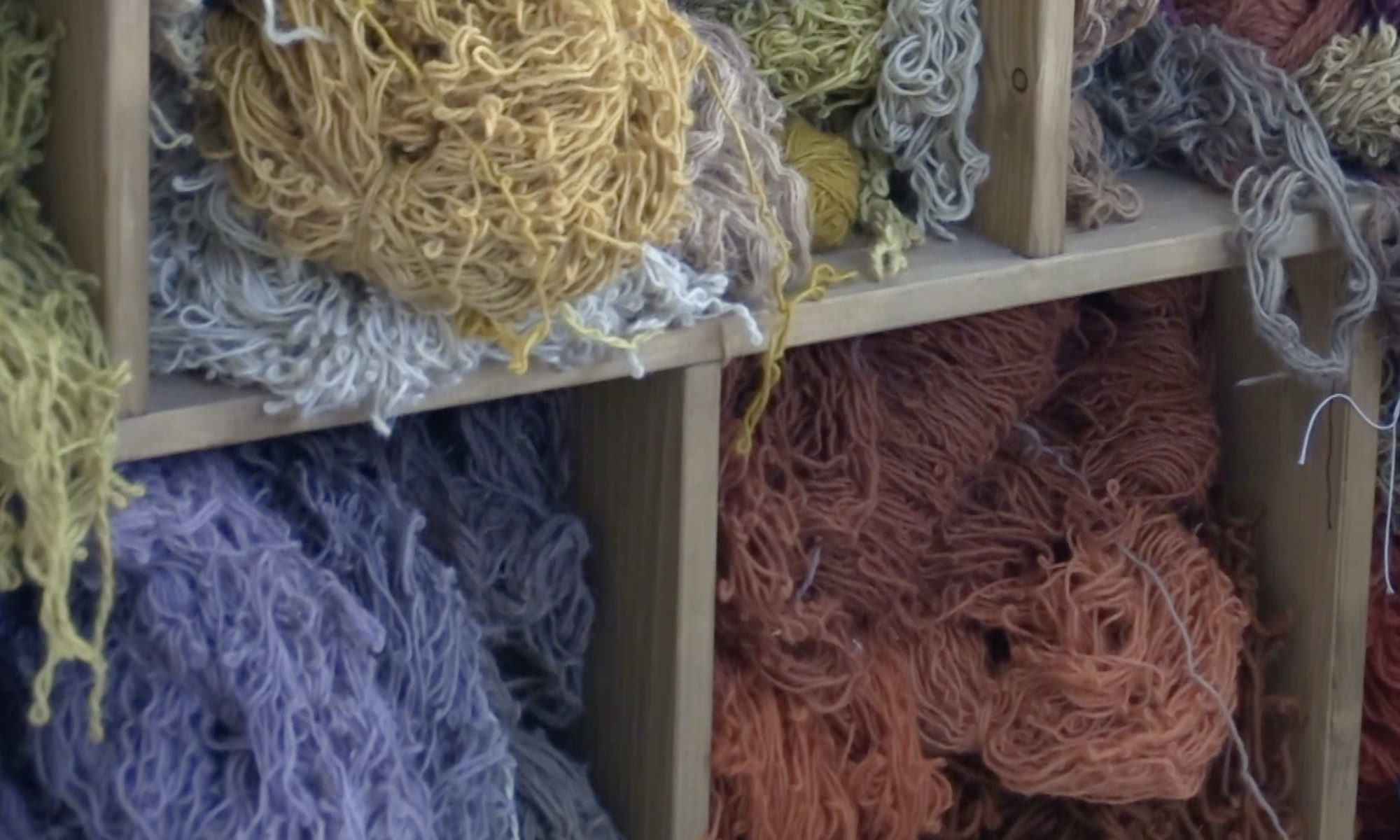
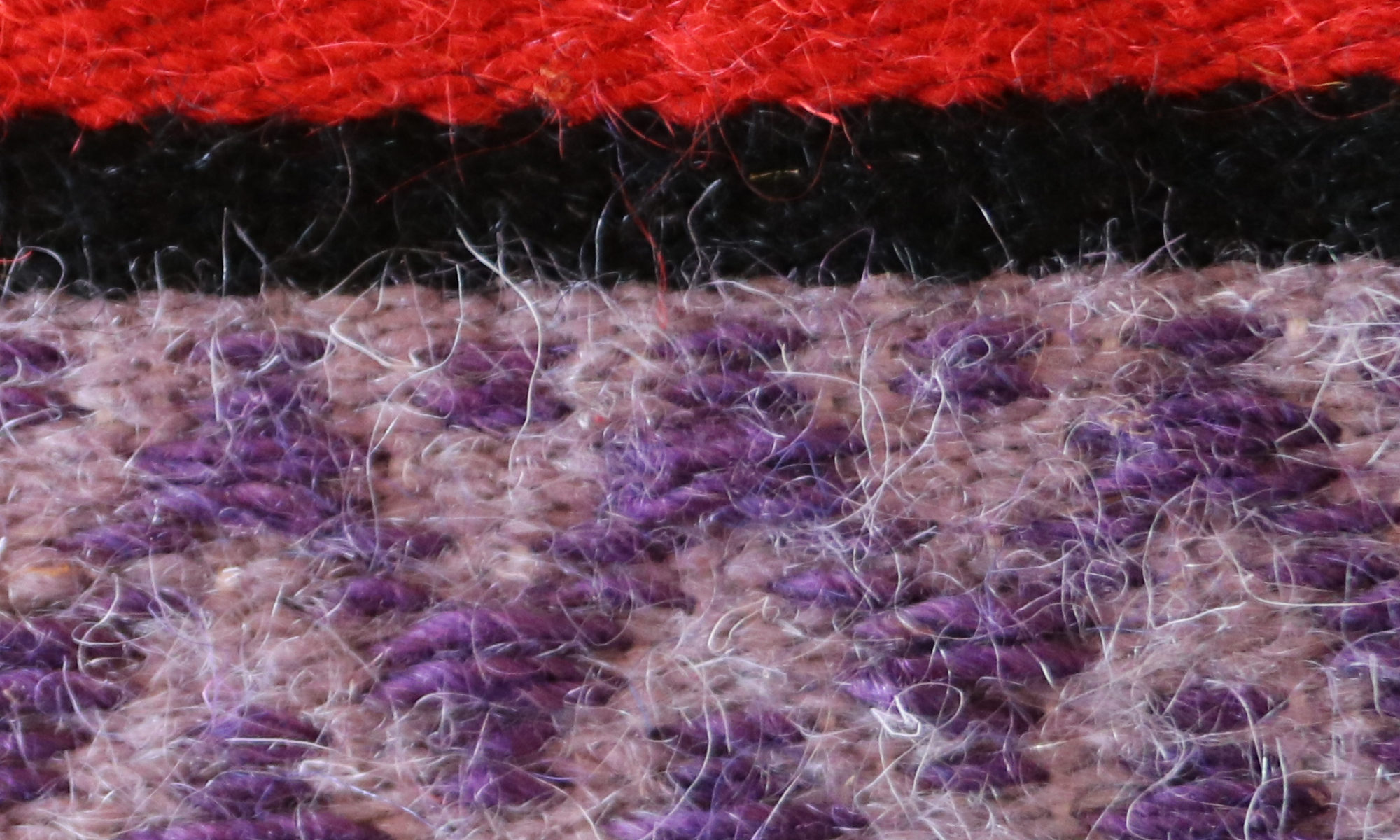
Gabriella Lutzu, shown here in her studio L’Albero Padre, exemplifies the art in Aggius, as she weaves rugs, wall hangings, bags, and more in her vibrant studio.
See a video of Gabriella at work in her studio.
Learn more on the page Gabriella Lutzu.
Watch a short video of Gabriella weaving in her Aggius studio.
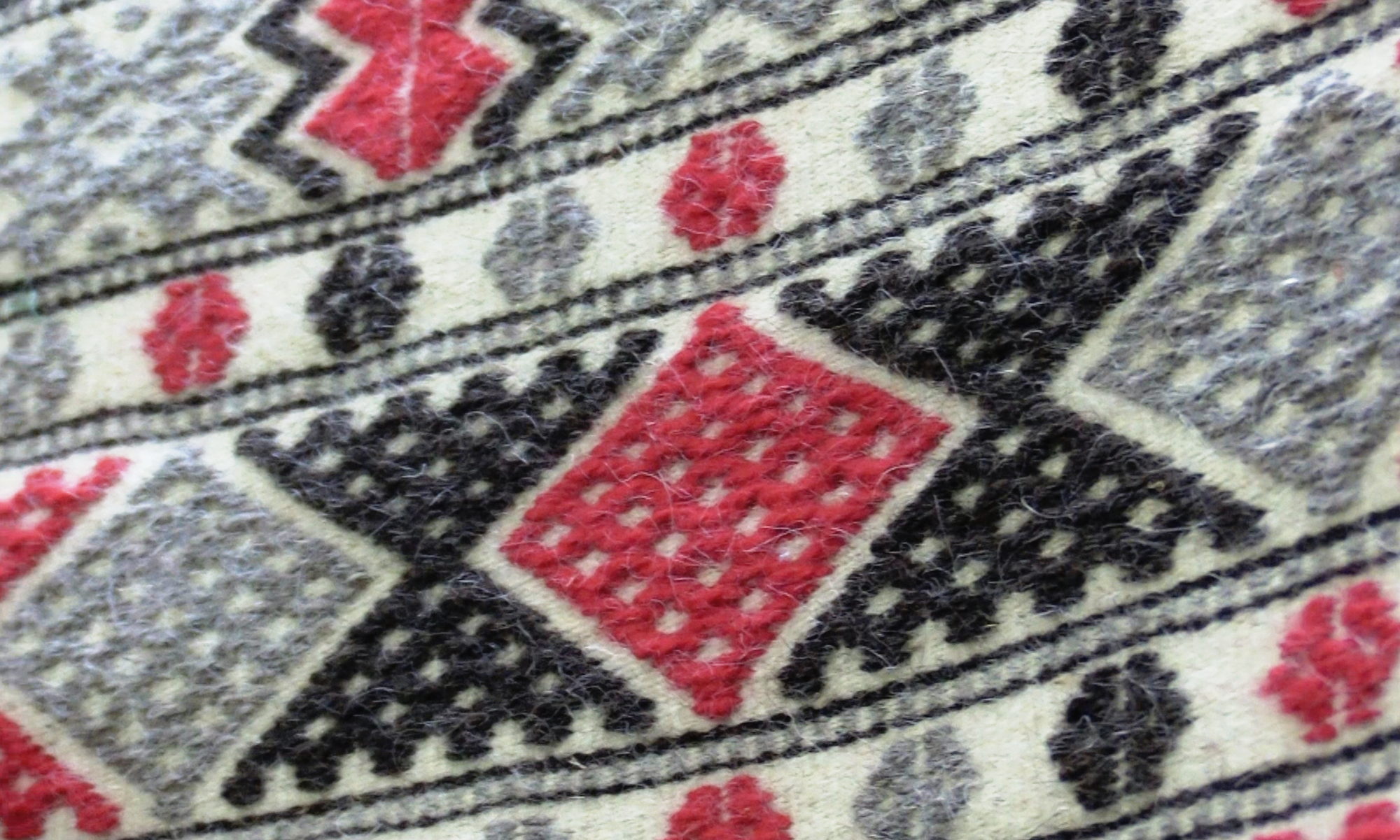
Map
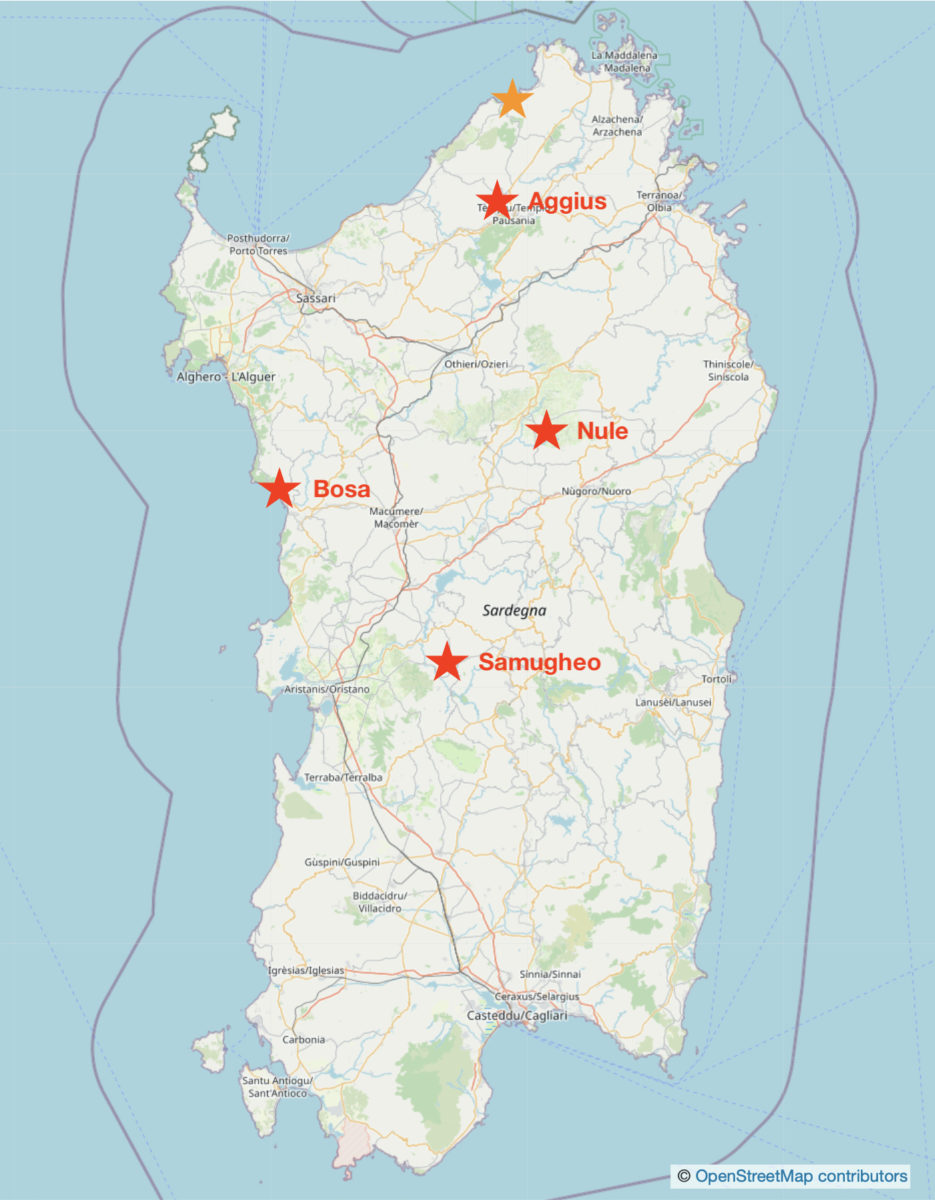
© 2013 – 2025 Kelly Manjula Koza | All Rights Reserved